Other Plastic Compounding
Polymers have been continuously replacing materials such as metal, glasses, and paper due to their flexible characteristics and low cost. There are thousands of formulae for different plastic applications.
Except the main purposes, there are many other types of plastic compounding for specific scenarios.
USEON always provide plastic compounders with the following processes.
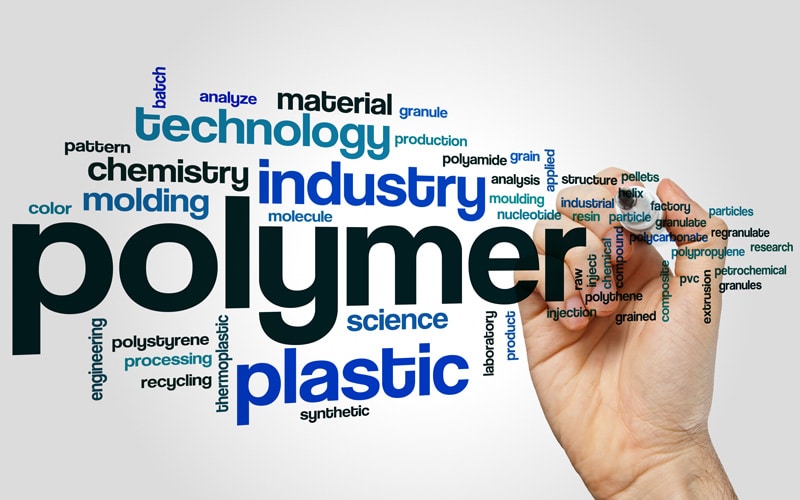
Table of Contents
Polymerization is a process of reacting monomer molecules together in a chemical reaction to form polymer chains or three-dimensional networks.
Devolatilization is the removal of volatile substances from a solid. It is one of the most important operations in polymer manufacture.
Tech Features & Advantages
a) We need extruder with long shaft 60–76L/D, even connect the two extruder in series to get enough residence time for reacting and enough zone for devolatilization.
b) 20~40% monomer molecules will be suck out by strong vacuum system with heat exchanger and collecting tank.
c) Oil heating for high precision control of temperature.
Please check the following Projects of PMMA polymerization and devolatilization.
Basic Formula:
PE/PP/PC/PA Compounding with color masterbatch and additives.
USEON have supplied 8 lines to producers, including the largest European distributor for rotational moulding material.
Single Screw Extruder for Coloring Process:
Special mixing zone for minimum waste during changing the color.
Special melting zone for high output and less average energy consumption.
Miller is with cooling jacket which can handle all kind of polymer without sticky.
Twin Screw Extruder for Crosslinkable PE:
Precise temperature control and appropriate screw design to avoid reacting during compounding process.
Typical applications for crosslinkable PE powder include diesel fuel tanks, chemical storage tanks etc.
USEON can supply the complete line from premixing system to miller.
Most Common Thermoset Types:
Epoxy, Phenolics, Bismaleimide (BMI), Fluoropolymers
Application:
- Automobile: Resisters, Drive Motors, Controls, Valve Covers, Oil Pans, Air Suspensions
- Electrical: Circuit Breakers, Motor Control, Centers, Generators, Switchgear, Control Cabinets
- Marine: Engine Covers, Personal Watercraft, Boat Access Covers, Motor Housing
Powder Coating
Process:
Precise temperature control and appropriate screw design to avoid reacting during compounding process.
Less clearance between screws with better self-cleaning, and very smooth surface of screw and barrel assures that materials do not adhere to surfaces, overheat and degrade.
Split barrel which be opened at up and down direction, for easy cleaning and maintenance.
USEON can supply the complete line from premixing system to crusher.
Basic Formula:
PP/PE/PVC compounding with wood fiber up to 65%, color masterbatch and additives
Application:
Profile for window and floor and contruction
Sheet for table and door
Process:
- PP/HDPE melting temperature is more than 170℃, so it is necessary to feed wood fiber from the side feeder.
- Wood fiber premix additives then feed into side force feeder. USEON supply screw design to avoid over shearing but still good mixing without reducing the length of fiber.
- For PVC window profile, no need to make compounding material into pellets, just cool down and crush it into powder.
USEON can supply the complete line from premixing to profile/sheet extrusion line.
Basic formula:
- EVA base: EVA, rosin, wax, stabilizer and additives
- TPU base: TPU (main) + others polymer (ABS/GPPS/EVA) + additives
Application:
Adhesive for car window, shoes, book and others.
There two process according to the viscosity of melting material:
1) If the viscosity of raw material is less than 4000CPS, it is better to use drop form pastillator system. The same system can be use for any additive material with melting temperature less than 100 degrees, such as wax, additives.
Distributor -> Belt Cooling System -> Bucket Elevator -> Packing System
2) If the viscosity of raw material is more than 4000CPS, it is better to use under water pelletizing system.
Loading -> Feeding -> Twin Screw Compounding -> Melt Filter -> Melt Pump -> Under Water Pelletizer -> Dewater -> Classifier -> Convey and Storing
Basic formula:
PP/PE, maleic anhydride (MAH), DCP, Acetone and other additives.
Application:
Coupling agent for PP compounding with Glass/carbon/wood fiber and mineral powder etc.
Compatibilizer for alloy compounding, such as PP/PA6, ABS/PA6, PA/EDPM
Process:
One loss -in-weight feeder for polymer.
Add MAH and DCP into solvent acetone and mixing by agitator. One loss in weight feeder for mixed liquid.
Need good vacuum system for degassing.
Water cooling strand pelletizing.