Filler Masterbatch
USEON provides advanced pelletizing line for all kinds of filler masterbatch.
We design the extruders for filler masterbatch, according to the output, formula and final application as your request.
Filler Masterbatch are concentrates of CaCO3 or Talc or BaSO4 in a polymer base.
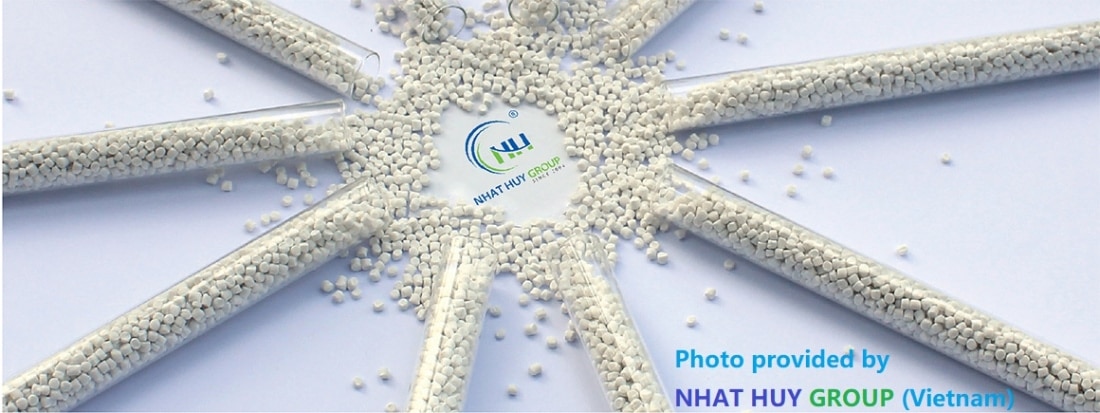
Table of Contents
The Basic Formula
Base Resin | Filler Type | Additives |
---|---|---|
PE | CaCO3 55-85% | PE wax |
PP | Talc 25-60% | White Oil |
PS | BaSO4 40~70% | Anti oxidant |
Applications
FILLER masterbatches are used in injection, blow-moulding, film(One layer or Multiple layer), sheet and tapes applications. They offer the following advantages:
a) Injection & blow-moulding
- Lower raw materials cost, as they are usually more economic than polymer resins
- Increased output due to faster mould cooling
- Reduction of colour masterbatch requirement
- Higher resistance to heat deflection, higher rigidity and stiffness
- Improved dimensional stability, weldability and printability
Addition rate of FILLER masterbatches in injection & blow-moulding applications can be up to 50 %, however, most usual levels are between 5-30 %.
b) Film, sheet, sacks, bags, raffia
- Lower raw materials cost, as they are usually more economic than polymer resins
- Reduction of colour masterbatch requirement
- Higher stiffness, paper-like effect
- Improved weldability and printability
- Improved anti-blocking properties
- Better bubble stability
Addition rate of FILLER masterbatches in film applications is 2-20 %.
c) PE & PP tapes
- Antifibrillation (also known as anti splitting)
- Lower raw materials cost, as they are usually more economic than polymer resins
- Reduction of colour masterbatch requirement
- Higher stiffness
- Improved weldability and printability
- Improved anti-blocking properties
- Improved weaving ability
- Easier processing
Usual addition rate of FILLER masterbatches in tapes is 3-8 %.
d) HDPE & PP Pipe
- Replacing expensive white masterbatch with its high white degree
- Lower raw materials cost, as they are usually more economic than polymer resins
- Higher stiffness
- Smooth pipes with lower coefficient of friction to better prevent them from blocking
- Being less possible to be brittel in low temperature due to its excellent cold resistance
Usual addition rate of FILLER masterbatches in tapes is 5-30 %.
Processing of Filler Masterbatch
a) Feeding System
There two feeding system:
Volumetric feeding system
- Weight the raw material separately according to the formula
- Then put all the material into high speed mixer for 5~10minutes mixing
- Discharge the material into spiral loader
- Loading the material into the hopper of volumetric feeder
Loss-in-weight feeding system (automatically and higher accuracy)
- Put the raw material into each tank on the ground.
- Vacuum loader will convey each component into the storing silo.
- The raw material will fall into the loss-in-weight feeder automatically. The feeding system will feed the material separately into extruder according to your formula setting one the HMI.
Loss-in-weight feeding system & Side Force Feeder
b) Technical Specifications of Extruder
According to your application & output, there’re many different choice on extruders.
Model | Diameter (mm) | Max. Speed (rpm) | Motor (kW) | L/D | Output (kg/hr) |
---|---|---|---|---|---|
SAT52 | 51.4 | 800 | 110 | 48-52 | 250-350 |
SAT65 | 62.4 | 800 | 160 | 48-52 | 450-600 |
SAT75 | 71.4 | 800 | 250 | 48-52 | 700-900 |
SAT95 | 93 | 600 | 600 | 48-52 | 1200-1600 |
Model | Diameter (mm) | Max. Speed (rpm) | Motor (kW) | L/D | Output (kg/hr) |
---|---|---|---|---|---|
SAT-T52 | 51.4 | 600 | 110 | 44-48 | 400-500 |
SAT-T65 | 62.4 | 600 | 160 | 44-48 | 600-800 |
SAT-T75 | 71.4 | 600 | 250 | 44-48 | 900-1100 |
Kneader + Single Screw Extruder
Model | Kneader Volume (Liter) | Screw Diameter (mm) | Screw Speed (rpm) | Motor (kW) | Output (kg/hr) |
---|---|---|---|---|---|
K75-TDD150 | 75 | 150 | 75 | 110/75 | 600-700 |
K110-TDD180 | 110 | 180 | 75 | 160/90 | 900-1100 |
Kneader + Twin Screw Extruder
Model | Kneader Volume (Liter) | Screw Diameter (mm) | Screw Speed (rpm) | Motor (kW) | Output (kg/hr) |
---|---|---|---|---|---|
K75-SAT75 | 75 | 71.4 | 600 | 110/132 | 800-900 |
K110-SAT95 | 110 | 93 | 400 | 160/200 | 1500-1700 |