Additive Masterbatch
USEON provides advanced pelletizing line for all kinds of additive masterbatch.
Additive Masterbatch is used in a wide variety of applications. For any type of plastic product, it needs at least two type of additives to modify the physical or chemical properties, such as flame resistance, thermal stability or weather resistance.
We design the extruders for additive masterbatch according to your requests and circumstances.
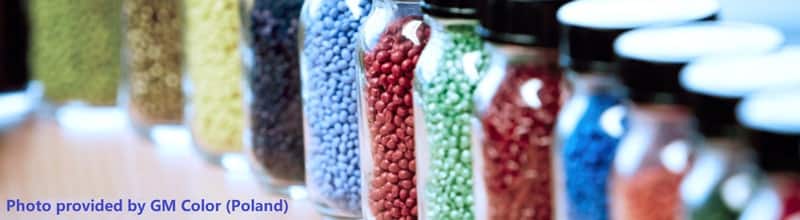
Table of Contents
Applications
a) Multilayer Films and Sheets
Polyolefins, PVC, PS, PA, PET, CPP, BOPP, BOPET and BOPA.
- Anti-oxidant
- Anti-slip
- Anti-static
- Anti-fog
- Anti-block
- IR absorbers
- Gas absorbers
- Gas barriers
- Slip
- UV stabilizers & absorbers
- Anti-root
- Anti-rodent
- Processing aid
- PIB
- Optical brightener
- Biodegradable additives
b) Engineering Plastics
SAN, ABS, PET, PBT, POM, PMMA, PA6, PA66, PC & all reinforced and modified polymers used in injection and extrusion applications.
- Anti-static
- Anti-oxidant
- Flame retardant
- Laser marking
- Mould release
- Processing aid
- UV stabilizers and absorbers
c) PET
APET, PETG, CPET & RPET used in injection moulding and extrusion and thermoforming applications.
- Anti-block
- Anti-oxidant
- Anti-scratch
- Chain extender
- Gas barriers
- IR absorbers
- Mould release
- Optical brightener
- Processing aid
- UV stabilizers and absorbers
d) Rigid PVC
Window profiles, Sills, Panels, Sidings, Gutters and Pipes.
- Anti-oxidant
- Mould release
- UV stabilizers & absorbers
e) 3-Layer PE Coating for Steel Pipes
- Anti-oxidant
- Adhesive
- Maleic Anhydride (MAH) Grafting
- UV stabilizers & absorbers
Processing of Additive Masterbatch
a) Feeding System
There are two types of feeding system:
Premix process with volumetric feeder
- Weigh the raw material separately according to the formula
- Then put all the material into high speed mixer for 5~10minutes mixing
- Discharge the material into spiral loader
- Load the material into the hopper of volumetric feeder
Split feeding by Loss-in-weight feeder: (automatically and higher accuracy)
- Put the raw material into each tank on the ground.
- Vacuum loader or liquid pump will convey each component into the storing silo.
- The raw material will fall into the loss-in-weight feeder automatically. The feeding system will feed the material separately into extruder according to your formula setting on the HMI.
There are three type of Loss-in-weight feeder for liquid, pellet and powder form materials.
Some additives are sensitive to shearing, so the best process is thus split-feed– feeding into the fifth barrel of extruder by side force feeder. Side force feeder is fixed with a water cooling jacket for additive powder with low melting temperatures.
b) Technical Specifications of Extruder
One extruder should be able to manufacture many types of additives. So, it needs fast cleaning type strand die plat for change of formula.
The bulk density of additive is relatively low, so the output is mostly depending on the feeding capacity, not the torque of main motor. So, our SAT twin screw extruder is more adapted for this process.
Technical Specifications of Extruder:
Model | Diameter (mm) | Max. Speed (rpm) | Motor (kW) | L/D | Output (kg/hr) |
---|---|---|---|---|---|
SAT40 | 41 | 600 | 45 | 40 | 150~200 |
SAT52 | 51.4 | 600 | 90 | 40 | 200-300 |
SAT65 | 62.4 | 600 | 160 | 40 | 400-500 |
SAT75 | 71.4 | 600 | 250 | 40 | 800~1000 |