PET Foam Core: A Better Alternative to PVC Foam Core
Table of Contents
What’s PET Foam Core
The main component of PET foam core material is polyethylene terephthalate, commonly known as polyester resin
PET foam is a kind of closed-cell thermoplastic structural foam. The PET foam core material has certain shear and compression strength. It is used as the core material of sandwich structure and is widely used in construction, road transportation, rail transportation, aviation, wind power and other fields.
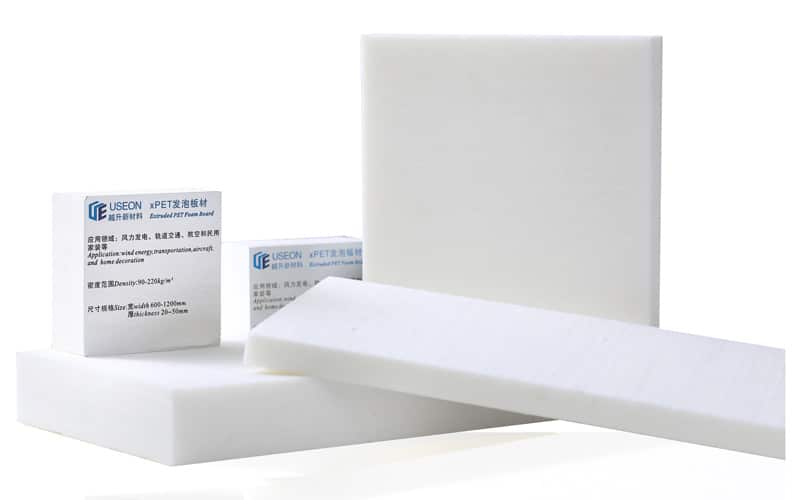
USEON PET Foam Core
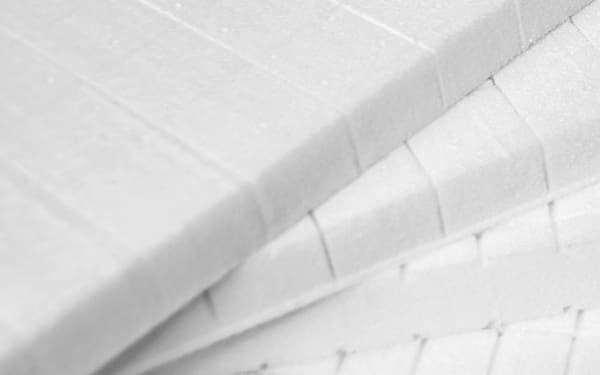
What’s PVC Foam Core
High expansion ratio rigid PVC foam board is a product formed by using PVC resin as raw material and foaming with a chemical foaming agent.
PVC foam core material has the following characteristics:
- Lightweight
- Closed cell
- High strength
- High bonding strength
- Flame retardant, etc.
PVC foam core was mainly used in aviation, marine and transportation industries. The main manufacturers are: 3A Composites, DIAB Group, CoreLite Composites, Gurit.
PVC Foam Core
Advantage of PET Foam Core
PET foam core material has the following characteristics:
- Convenient processing: through thermoforming, a complex body structure can be realized, and the thermal stability is good under heating. It is convenient to use most types of resins and production methods for processing.
- Good mechanical properties: excellent mechanical properties, good compressive strength and high shear modulus.
- High temperature resistance: It can withstand a temperature of about 150°C for a short time during the processing, and can withstand a temperature of about 100°C for a long time during the service life.
- The production process is environmentally friendly: Traditional PET foam uses fluoride as a foaming agent during production, which will have a certain impact on the environment and human health. However, the latest PET foaming technology can use the carbon dioxide generated during the production process as a foaming agent. Conducive to environmental protection.
- 100% recyclable: scraps and chips can be reused in the production process. Waste PET foam core materials are also easy to recycle.
Why PET Foam Core Can Be PVC Foam Core Alternative
PVC foam core material is also a material commonly used in wind turbine blades. But now, PET foam core material has begun to gradually replace the use of PVC foam core material.
There are two main reasons:
Compared with PVC, PET is more environmentally friendly
The waste treatment of PVC is mainly burning and burying, which causes certain pollution to the soil and air. And PET is a material that can be 100% recycled.
Especially with the rapid development of the wind power industry, the demand for wind blade core materials has also surged. Choosing a new type of PET core material is a more environmentally friendly choice.
PET foam also has higher performance than PVC foam
The material of the fan blade has strict requirements on density, water absorption, tensile strength, compressive strength, shear strength, bending strength, and bending fatigue performance.
In these indicators, PET foam has certain advantages over PVC foam.
The high temperature resistance of PET foam is better. Therefore, in the processing process, PET foam is less prone to discoloration or even carbonization, and the yield rate of fan blades is more guaranteed.
Taking Armacell ArmaForm® PET as an example, the performance comparison chart of PET foam and other core materials such as PVC and Balsa is as follow image:
Image Source: Armacell Brochure
Not only in the wind power market, PET foam core materials are also popular in the fields of construction, industrial manufacturing, shipbuilding, aerospace, and rail transit.
In these areas, it can also be a good alternative for traditional PVC foam core.
Application of PET Foam Core
Wind power industry
- Wind blade shear webs and shell
- Nacelles covers
- Composite sandwich structural parts
Under the new energy trend, PET foam used in the wind power industry is the largest increase. The main purpose of the newly-added PET foam production line in China is this aspect.
Transportation industry
The use of PET foam board as a composite core material, from cars to trucks, from buses to trains and airplanes, can reduce weight by up to 50%, reducing fuel consumption and carbon dioxide emissions.
Mainly used for vehicle floor, side wall, body structure, internal structure, roof, etc.
Marine
Boats/Ships Deck, internal structure, superstructure.
Building industry
PET foam board can provide unparalleled freedom for design and construction.
Other advantages such as low thermal conductivity, easy installation, light weight, long free span, feasibility of combining with various types of decorative surfaces, anti-corrosion, low maintenance and repair costs, become building designers and engineers to replace existing buildings Preferred choice of materials.
It is widely used in roofs, claddings, domes, mobile houses, supporting templates, etc.
Other industries
Covers, containers, X-ray tables, sports equipments.
How to produce PET Foam Core
Based on the polymer processing technology assisted by supercritical fluid (SCF), extrusion foaming process, coupled with the reactive extrusion of PET which is facilitated by the plasticization effect of SCF, is developed to produce xPET board foams.
Both of virgin and recycled PET could be used as raw materials and supercritical fluid is used as physical blowing agent.
In order to avoid the strong hydrolysis of melt PET, all materials should be dried first by hot air with dew point of at least -40oC for 4 hours, with the purpose of eliminating the humidity below 50ppm.
PET and additives are fed at constant rates through gravimetric dosing devices. The reactive extrusion of PET with multifunctional agent increases the molecular weight, broadens the molecular weight distribution, and introduces long-chain branch, which increases the melt foamability of PET and the product properties.
The blowing agent, injected into the extruder steadily, dissolves into the PET melts in the extrusion line, and the PET/SCF solution is then cooled and extruded through the foaming die, where cells nucleation and growth are initiated by the rapid depressurization.
The extruded PET foams are then calibrated, conveyed, edge cut, and surface planed to obtain the final xPET products.
The xPET production line designed and constructed by USEON team could improve the productivity efficiently, reduce production cost, and regulate the xPET properties easily.
How to buy PET foam Core
Globally, currently the main brands of PET foam core materials that can be selected are as follows:
- Diab’s Divinycell P
- Armacell’s ArmaForm® PET
- AIREX® T10 / T90 / T92 from 3A
- Composites Group
- Owens Corning WINDCORE® 100
You can also contact us, our customers use our pet foam core production line to make products that are comparable to the quality of these major international brands.