Sheet Direct Extrusion Line
Using USEON Direct Extrusion technology, it is possible to take multiple raw materials such as polymer, filler, and additives mixed or split feed, reacted, and devolatilized in a high-speed co-rotating twin screw extruder, to directly produce high quality finished products, such as sheet and film, without the need for pelletizing.
We have completed many Direct Extrusion projects, solving several problems normally encountered using traditional processing methods. We would like to share our Direct Extrusion experience below.
Table of Contents
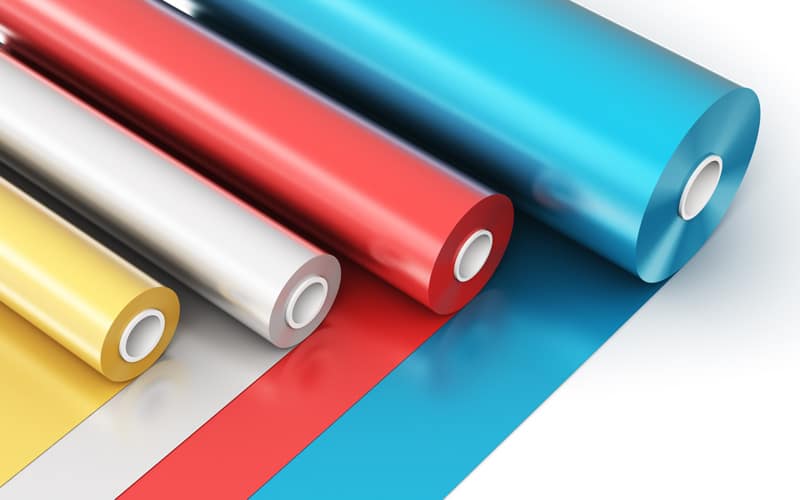
Why Direct Extrusion
Traditional Process for Film/Sheet:
- For simple formulations, such as PE with small added quantity of masterbatch/additives
The process: premix all components and add into the single screw extruder for sheet/film extrusion. - For complicated formulas, such PP with 40% filler/wood fiber
The process: the first step is processing the filler or wood plastic by compounding in a twin screw extruder. Following that premix all components and add into the single screw extruder for sheet/film extrusion. - For water sensitive material, such PET/PA
For this process: 3-5 hours of pre-drying is necessary before extrusion by single screw extruder.
Disadvantages of traditional processing methods:
- More energy consumption for pre-dry or two stage process or single screw extruder
- More manpower, factory space and investment
- Less dispersion quality for additive and polymer in different MFI
- Overheating and shearing for natural wood fiber
- Over shearing for Glass fiber in D-LFT process
- Polymer degradation in two step process
Experience in Direct Extrusion
1) PP Compounding with Talc and Sheet Extrusion
Basic Formula:
COPP Compounding with 40% Talc and 2% Color masterbatch.
Sheet Specification:
Width: 850mm
Thickness: 0.6 – 1.0mm
Linear speed: 10 – 17m/min
Maximum output: 900kg/h
Application:
thermoforming for food packing
Process:
Vacuum loading and split feeding system to avoid dust pollution on final sheet.
PP and Color masterbatch are feed into the first barrel.
Talc is separately fed into two side force feeders.
There is no lubricant additive because the final sheet is used for hot food packing. When the output of extruder more than 600kg, the melting temperature will increase due to friction. USEON supply a special cooler and screw design to reduce the melting temperature before T-Die.
Sheet extrusion can be linked to the thermoforming line, bypassing the winder, eliminating the need for a preheating system when thermoforming, which saves energy and manpower.
USEON can supply complete DIRECT EXTRUSION lines from feeding to thermoforming.
Basic Formula:
PP Compounding with 40% wood fiber, color masterbatch and additives
Sheet Specification:
Width: 1400 – 1600mm
Thickness: 0.8 – 1.5mm
Linear speed: 4 – 10m/min
Maximum Output: 600kg/h
Sheet Application:
Protection layer of wall and ceiling panel
Process:
PP and Color masterbatch are feed into the first barrel.
Wood fiber premix additives then feed into side force feeder. PP melting temperature is more than 190℃, so it is necessary to feed wood fiber after PP melt.
USEON supply screw design to avoid over shearing but still good mixing without reducing the length of fiber.
Due to low fluidity of wood fiber, USEON have developed a special gear pump and suggest one type of inner lubricant.
The final sheet will be sticky on the natural wood panel so non-woven fabric coating for both sides.
USEON can supply the completely DIRECT EXTRUSION line from feeding to stacker.
3) HDPE Waterproof Sheet
Basic Formula:
HDPE Compounding with color masterbatch and additives
Sheet Specification:
Width: 1200 mm ± 2 mm
Thickness: 0.65 – 1.40 mm ±0.05mm
Linear speed: 8 – 17m/min
Maximum output: 800kg/h
Application:
Floor Moisture Barrier & Roofing Underlayments
Process:
Vacuum loading — gravimetric feeding — twin screw extruder for sheet extrusion.
Twin Screw Extruder Advantage:
Comparing to single screw extruder, twin screw extruder have the following advantages:
- Saving energy up to 30%
- Better dispersion performance
- Less waste for changing color due to self-cleaning effect
- Less residence time leads to less polymer degradation
USEON can supply the completely DIRECT EXTRUSION line from premixing to winder.
4) BOPP Film Extrusion
Basic formula:
PP compounding with additives (anti-slip, anti-static, anti-oxidant)
Application:
For all kind of packaging
Film structure:
A/B/A
Process:
Traditional process is two sets of single extruders with series connection to get more output.
We replace two sets of single screw extruder into one set of twin screw extruder.
Advantages:
Energy saving up to 30%: the same motor 1200KW, we can reach an output 5500kg/h, while a single screw extruder can only reach maximum 4200kg/h.
Less residence time leads to less polymer degradation.
Better dispersion performance leads to lower percentage of additives
Better degassing performance.
Technical Specifications of Extruder:
Model | Diameter (mm) | Max. Speed (rpm) | Motor (kW) | L/D | Output (kg/hr) |
---|---|---|---|---|---|
SAT-X150 | 150 | 400 | 1200 | 36 | 5000-6000 |
SAT-X175 | 175 | 300 | 2000 | 36 | 7000-10000 |
5) EVA Film for Solar Cell Encapsulation
Basic Formula:
EVA (TPC MA-10 with VA content <=33), additives in liquid or powder form
Sheet Specification:
Width: 2300 mm
Thickness: 0.2~0.9mm (with accuracy +/-0.02mm)
Shrinking rate: <3% Linear speed: > 6m/min
Maximum Output: 500kg/h
Application:
Solar Cell Encapsulation
Process:
EVA and additive are premixed and feed into the first barrel by loss in weight feeder.
Liquid additives are fed into the 4th barrel by loss in weight feeder.
Special screw design assures good mixing and avoids over shearing.
Better degassing performance.
Hot calibration system to reduce shrinkage rate.
Automatic winder with Tension control system (tension range:10~100N).
USEON can supply the completely DIRECT EXTRUSION line from feeding to winder and including the on-line crushing system.
Basic Formula:
PVB/SGP, additives and on line waste material
Sheet Specification:
Width up to 4000 mm
Thickness: 0.3~1.5mm
Output: 300~600kg/h
Application:
Laminated Glass for Automotive and Building
Process:
Special cooling jacket for feeding system to avoid the choking due to the sticky of raw material.
Twin screw extruder for better mixing and degassing performance.
Co-extrusion for two color (on the edge)
Automatic T-die interlock with thickness tester.
USEON can supply the completely DIRECT EXTRUSION line from feeding to winder, including the on-line crushing system.